일반적인 구조물의 설계는 주어진 설계하중(고정하중, 활하중, 풍하중, 지진하중 등)을 일정한 상태(탄성상태, 한계상태)내에 저항할 수 있도록 설계한다. 일반적인 구조물의 설계법은 강도설계법, 허용응력설계법, 한계상태설계법 등 정형화된 설계법에 따라 설계할 수 있다.
도로안전 시설의 경우 차량의 충돌하중에 따른 충격력을 소산시키거나 도로밖으로 이탈하지 않도록 방향을 선회시키는 역할을 하는 구조물로 도로의 분류(고속도로, 국도) 및 충돌차량에 따른 성능 기준을 마련하여 충돌시험을 통한 구조성능 및 탑승자 안전성능을 만족해야만 한다.
충돌하중은 충돌 차량의 조건 뿐만 아니라, 구조물의 형상 및 강성 등에 따라 변하게된다. 따라서, 정형화된 설계법이 없으며 충돌하중에 대한 이론적 산정방법과 메카니즘 해석을 통해 방호울타리의 강도 초기 설계과정에서 검토해보는 정도이다.
이러한 도로안전 시설의 특성상 시행착오를 통해 구조 및 제원을 수정하는 방법이 일반적인 설계방법이다. 도로안전시설의 충돌시험을 통한 성능 검증이 1990년대 후반 부터 실차충돌시험을 실시해오고 있어 제작사들의 노하우를 기반으로 개발하고 있다. 충돌시험을 통과하는 확률은 30~40% 정도(2012년 기준)로 제품 하나를 개발하기 위해 평균 3번의 충돌시험을 실시한다. 충돌시험 비용의 경우 소형차와 대형차에 대해 각 1회 실시하는데 시험수수료, 자재비, 시공비 및 부대비용을 포함하면 약 1억원 정도 발생함을 고려하면, 개발비용이 상당함을 알 수 있다.
이렇게 막대한 개발비용과 시행착오를 줄이기 위한 방법으로 가장 대표적인 것이 충돌시뮬레이션을 통해 구조성능 및 탑승자 안전도를 예측해보고 개선점을 찾아 시스템을 개량하는 방법을 사용한다.
시뮬레이션을 통한 도로안전시설의 개발은 해외에서 널리 사용하는 방법으로 미국의 경우 Texas Transportation Institute, Southwest Research Institute, Midwest Roadside Safety Facility, National Crash Analysis Center 등 많은 기관에서 사용하고 있으며 실물차량 충돌시험과의 비교와 캘리브레이션을 통해 높은 신뢰도를 보이고 있다.
유럽의 경우 표준위원회(CEN)에서는 실물차량 충돌시험을 통해 성능이 입증된 도로안전시설의 경우 소소한 구조적 변경이 발생하는 경우 충돌시뮬레이션을 통한 성능평가로 실물차량 충돌시험을 대체하도록 하고 있다. 이 경우 충돌시뮬레이션은 CEN/TC 226에 제시된 기준에 부합해야 하며 탑승자 보호성능(THIV, ASI)의 경우 오차범위가 10% 이하로 한다.
국내의 경우도 충돌시험과 시뮬레이션의 캘리브레이션을 통하여 신뢰성의 확보가 이루어지고 있으며, 대표적인 사례로 국책연구과제인 Smart Highway 사업단의 연구에서 방호울타리 개발에 충돌시뮬레이션을 활용하였고, 시뮬레이션 결과가 실물차량 충돌시험과 매우 유사한 거동을 보였다. 이 과제에서는 중앙분리대 및 노측용 가드레일에 대한 기준 제정을 위해 다양한 충돌조건에 대한 실물차량 충돌시험을 총 10여회 실시하였으며, 이중 최종 선정된 기준안에 대한 성능평가 시험은 100%의 성공율을 보였다. 일반적인 성공률이 30~40%인 것에 비해 매우 높은 성공률을 보여 막대한 예산을 절감한 사례가 있다.
이처럼 충돌 시뮬레이션의 신뢰성이 확보된다면 많은 비용과 개발 시간을 절약할 수 있는 방법이다.
그러나 구조물을 모델하고 해석하는 개발자의 풍부한 경험과 입력자료가 적절하지 못한다면 신뢰성을 확보하기 매우 힘들다.
충돌시뮬레이션의 신뢰성 확보를 위해서는 다음과 같은 사항들을 고려해야 한다.
1. 적절한 모델링 및 요소의 선정
시뮬레이션의 신뢰성을 확보하기 위해서는 기본적으로 구조물을 적절하게 모델링해야 하고 사용되는 다양한 해석 요소중 적당한 요소를 선택해야 한다. (Shell 요소만 해도 20여 가지의 해석 모델이 존재한다.)
2. 재료 모델
일반적으로 도로안전시설의 모델에 사용되는 재료는 강재, 알루미늄, 목재, 콘크리트 및 지반(흙) 등 이며 각 재료에 대한 역학적 특성을 실제와 유사하게 반영할 수 있어야 한다.
강재의 경우 일반적인 설계에 사용되는 항복강도 및 인장강도는 최소강도(Garunteed strength)를 사용하여 실제 인장강도 시험을 실시하면 더 높게 나오게 된다. 구조물을 탄성상태로 설계하는 경우 크게 문제가 되지 않지만 도로안전시설의 경우 항복강도를 넘어 소성상태에 다다르게 되고 파단까지 고려해야 하기 때문에 실제 재료의 항복강도 및 인장강도를 고려해야만 한다. 이를 위해 시편 인장시험을 실시하여 보정하거나 부재 시험과 시뮬레이션을 통해 입력변수를 적절하게 수정한다.
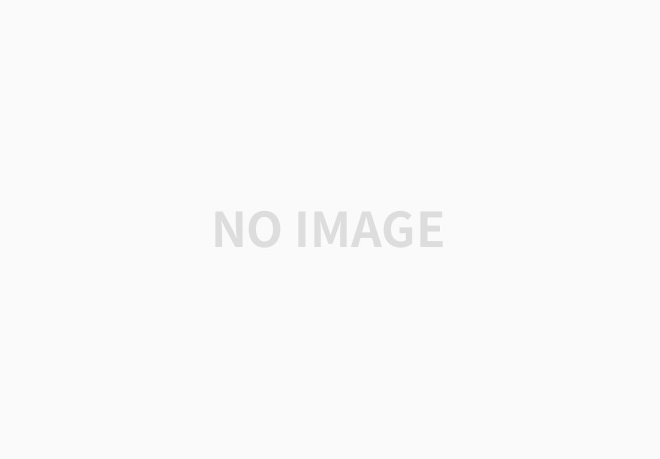
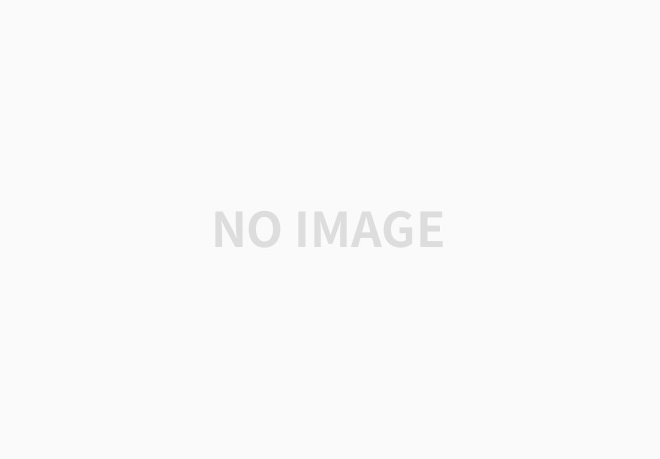
3. 지주 및 지반 상호작용
대부분의 차량방호울타리는 지주가 지중에 매입되는 형태로 지주 및 지반의 상호작용에 대한 거동을 규명하여 시뮬레이션의 입력자료로 활용해야 한다. 특히 지반의 경우 거동이 복잡하고 지주에 따라 지반의 반력계수의 차이를 보이며, 횡방향 지지말뚝에 사용하는 설계이론들을 참고하여 적절한 지반반력을 모사해야 한다.
이렇게 산정된 지반특성은 실제 거동과의 비교가 필요하며 적절한 파라메터의 수정을 통해 실제와 유사한 거동을 나타내도록 해야한다. 지반모델의 경우 Solid 요소를 사용하고 지반의 물성값을 입력하여 모델링 하는 경우와 지반을 탄-소성 스프링으로 치환하여 사용하는 경우가 일반적이다.
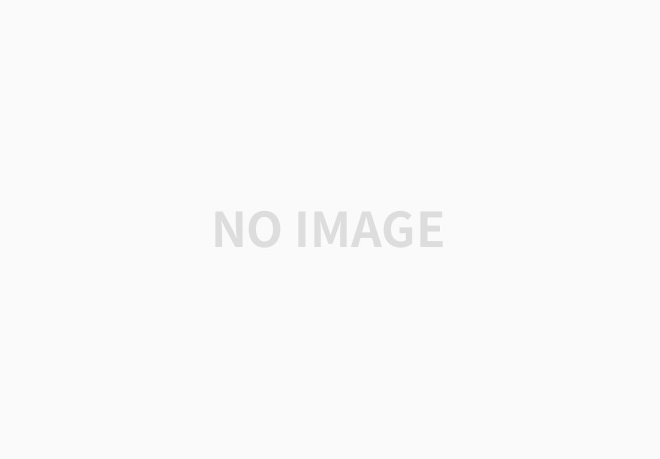
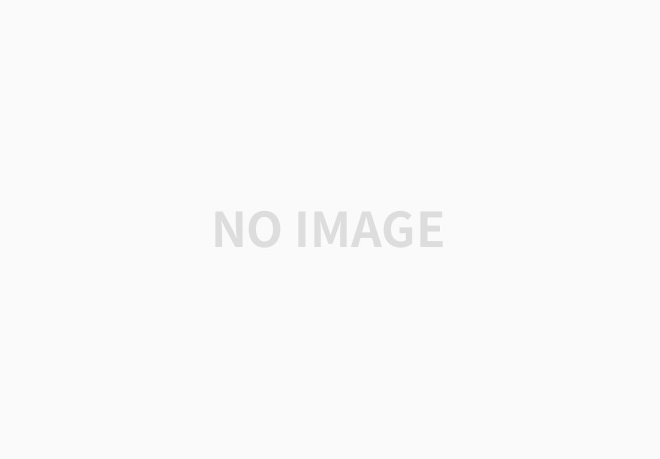
4. Strain Effect 고려
충돌하중을 받는 구조물의 경우 재료의 강도는 재하속도에 따라 증가하게되며 이러한 효과를 Strain Effect라고 한다. 이러한 경우 기존의 정적시험에 의한 재료의 강도에 비해 증가하게 되며 이러한 효과는 전체적인 구조물의 거동에 영향을 미치게된다.
차량방호울타리의 특성상 높은 Strain rate의 재료 거동을 보이며, 강재의 Strain rate에 대한 정확한 연구가 미미하고, 입력 변수로서 정확히 모델하는데 한계를 보이기 때문이다. 기존 연구결과(Amy E. Wright, 1996)에 따르면 Strain rate에 따라 재료의 강도가 2배 가까이 상승할 수 있다. 재료의 Strain rate를 고려하는 방법으로는 Cowper-Symonds의 식과 Simplified Johnson-Cook의 식으로 표현이 가능하나, 실제 시험 결과를 정확히 모사하는데 한계를 보이는 것으로 Michael Dietenberger 등(Michale Dietenburger, Murat Buyuk, Cing-Dao Kan, 2005)의 연구에 나타났다.
기존의 연구 결과를 살펴보면 Amy E. Wright의 연구에서는 미국 가드레일 재료인 AASHTO M-180 강재에 대한 연구결과 M-180의 정적시험에 의한 항복강도는 400MPa이나 50mm/sec의 재하속도에서는 650MPa 정도의 항복강도를 보여 약 60%의 강도가 증가를 보였다. 자동차에 주로 사용하는 DQSK Mild Steel에 대한 시험(Cady, C.M. et al, 2003)에서는 정적 항복강도는 270MPa이나 100mm/sec의 재하속도에서는 약 480MPa, 1000mm/sec의 재하속도에서는 약610MPa의 항복강도를 보여 각각 78%, 126%의 강도 증가를 보였다.
이처럼 기존의 연구결과를 참고하여 Strain Effect를 고려한 재료모델을 선정해야 한다.
5. 마찰의 영향
차량과 도로안전시설의 충돌시 차량과 지면의 마찰, 차량과 구조물과의 마찰 및 구조부재 상호간의 마찰 등의 영향에 따라 차량의 거동이 변화하게 된다. 일반적으로 마찰을 고려하는 방법으로는 Coulomb의 법칙에 의한 것이 있으나, 사용에 몇 가지 제한이 있다. 큰 하중에 의해 큰 접촉압력이 작용하여 실 접촉 면적이 외관접촉면적에 수렴해 가는 경우 및 고정된 항복점을 가지고 있지 않는 탄성 및 점탄성 재료의 경우 등이다. 또한 마찰공학(Bhushan, B,1998)에서는 양 표면간 거리가 단위 원자 간격 이내로 근접되면 두 금속체간에는 아주 강한 결합(응착)이 이루어 지는 응착이론에 의하면 접촉부위의 소성변형과 표면경화 현상에 의해 강한 결합상태를 이루게 된다. 접촉하던 두 물체를 강제로 분리시킬 경우 접촉면의 돌기부의 전단강도가 마찰에 영향을 주며 접착부의 재료가 연성이 클 경우 접합부 성장효과에 의해 마찰력이 증가한다. 따라서 적절한 마찰력이 고려되지 않으면 시뮬레이션 결과는 실제 충돌거동과 상이하게 된다.
6. 시뮬레이션의 안정성
차량과 구조물 상호간의 충돌거동에 대한 시뮬레이션의 경우 높은 압력이 상호간에 작용하게 된다. 이렇게 높은 압력에서 발생하는 Contact의 경우 요소간의 간섭, Hourglass 등이 발생하게되므로 요소의 세분화, 해석요소의 변경, Contact 방법의 변경 및 Control 옵션 등을 사용하여 해석을 안정성을 확보해야 한다.
위와 같은 항목들에 대해 적절한 파라메터들을 결정할 수 있다면, 시뮬레이션의 신뢰성을 확보할 수 있게된다.
아래 그림과 같이 노측용 차량방호울타리의 경우를 살펴 보면 동일한 충돌조건에 대해 시뮬레이션을 수행한것이다.
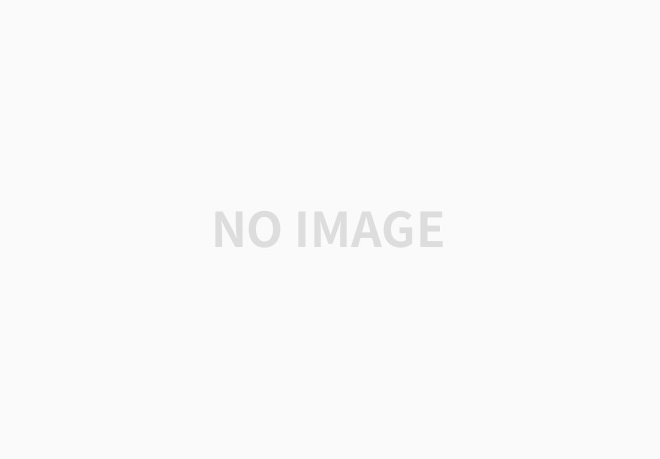
승용차의 충돌의 경우 탑승자 보호성능을 확인하는 시험 및 시뮬레이션으로서 차량 무게중심점의 3축 가속도 및 각속도를 계측하여 탑승자 보호성능(THIV, PHD 및 ASI)을 계산하게 된다. 아래 그림은 탑승자 보호성능에 가장 많은 영향을 미치는 차량의 횡방향 가속도를 비교한 것으로 최대 가속도는 시뮬레이션에서 약 4.7% 작게 나타났다.
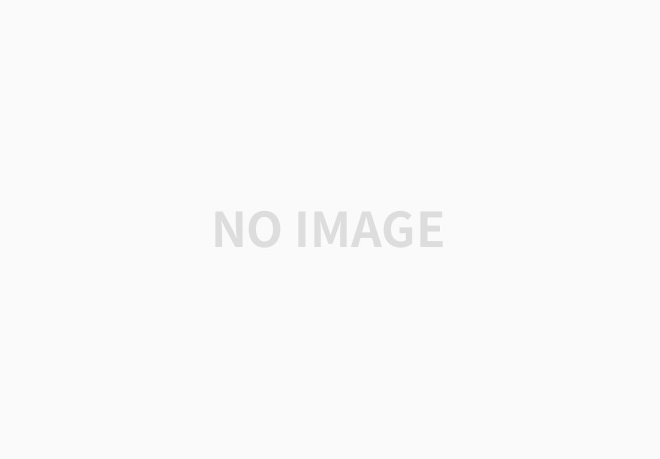
획득한 데이터로부터 탑승자 안전도 및 충돌 후 차량거동을 비교하면 아래표와 같으며, 탑승자 안전도에서 가장 중요하고 지배되는 THIV의 경우 시뮬레이션이 3.9% 크게 예측되며, PHD의 경우 36% 크게 예측된다. 여기서 THIV의 경우 가속도 데이터를 적분하여 차량과 탑승자의 상대속도로 계산되는 항목으로 노이즈의 영향이 적으나 PHD의 경우 가속도 데이터를 사용함으로 시뮬레이션에서 발생한 고주파의 노이즈가 반영되어 상대적으로 크게 예측된다.(필터링 조건을 변경하면 오차는 감소함) 이탈 속도 및 이탈각도의 경우 측정 위치와 측정 방법에 따라 변화하나 일반적으로 탑승자 안전도에 비해 오차가 크게 나타난다.
<결과 비교>
항 목 |
기 준 |
Test |
Simulation |
Error(%) |
탑승자 보호성능 |
THIV 33㎞/h 이하 |
27.6㎞/h |
28.9㎞/h |
+3.9 |
PHD 20g 이하 |
8.7g |
15.9g |
+36 |
|
충돌 후 차량거동 |
차량의 전도 등이 없을 것 |
없음 |
없음 |
- |
이탈속도는 충돌속도의 60% 이상 |
72.9㎞/h (57.5%) |
81.2㎞/h (80.60%) |
+13.7 |
|
이탈각도는 충돌각도의 60% 이하 |
11.5° (57.5%) |
10.2° (51%) |
-10.8 |
이처럼 충돌 시뮬레이션을 통한 도로안전시설의 검토는 수행자의 능력과 모델의 정확성에 따라 충돌시험의 시행착오를 줄이거나 기존 시설의 개량에 중요한 정보를 제공할 수 있다.
'References(자료실) > 충돌 시뮬레이션(Simulation)' 카테고리의 다른 글
가드레일 전이구간 충돌 시뮬레이션(반강성~강성 방호울타리) (0) | 2021.04.13 |
---|---|
차량방호안전시설에서의 시뮬레이션 활용과 신뢰성 검증 (0) | 2021.01.31 |
Bolt Preload(볼트 초기 축력) (0) | 2021.01.27 |
Perimeter Barrier Impact Simulation (0) | 2021.01.18 |
CC4(120km/h, 1300kg) Crashcushion Simulation (0) | 2021.01.05 |